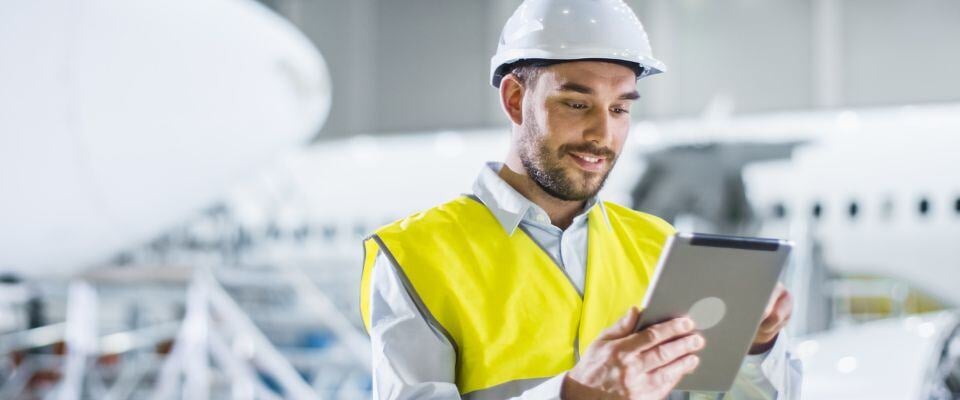
Ultimate Guide to Digital-Led Maintenance: Implementation and Overview
Table of Contents
- What Is Digital-Led Maintenance?
- What Is The Purpose Of Digital-led Maintenance?
- What Are The Advantages Of Digital-Led Maintenance?
- What Are The Disadvantages Of Digital-Led Maintenance?
- How To Create A Business Case For Digital-Led Maintenance In Your Organisation
- How To Implement Digital-Led Maintenance In Your Organisation
- Can Digital-led Maintenance Be Used On Its Own?
If you’ve heard of the term “Digital-led Maintenance” (DLM) before, it’s likely that you’ve come across several different industry interpretations.
Digital-led Maintenance is a broad approach that encompasses a wide range of digital technologies that transition data from the design and build stage through to a building’s operational phase.
At SFG20, it’s essential for us to keep you up to date and informed about new approaches to maintenance in order to fulfil our mission of making buildings safer and forging the way for industry wide operational excellence.
That’s why we've collaborated with DLM expert David Hemming CEng FICE FCMI FIWFM to bring you the most detailed and precise information possible. With over 30 years of experience working in the construction and property sectors around the world, David Hemming is a Service Delivery Lead at NHS Shared Business Services and a Chartered Civil Engineer.
By the end of this extensive guide, you will understand what Digital-led Maintenance is, alongside the pros and cons and how you can practically introduce it into your organisation.
What Is Digital-led Maintenance?
DLM is a combination of multiple technologies from collecting primary sources of data so it can be validated against expected performance, to how those data streams are captured and collated together.
Digital-led maintenance also incorporates how the data is then filtered and analysed, and how that data is then converted into usable information to help inform decision making.
It incorporates the software, data manipulation techniques and the technology that are required to process and analyse the data, from Building Information Models to Integrated Workplace Management System (IWMS) to the use of machine learning and Artificial Intelligence (AI) to assist in data analytics.
The concept of Digital-led Maintenance (DLM) has largely come from the manufacturing sector where organisations have looked to embrace digitisation and big data to reduce human error associated with heavily paper-based operating and maintenance procedures.
What Is The Purpose Of Digital-led Maintenance?
The more complex buildings and their associated services become, the greater the requirement for thorough and detailed maintenance.
The next challenge when it comes to maintaining and sustaining complex systems is to try and remove inconsistencies, deviations and omissions such as incorrect data.
It does not matter how well-trained or motivated individuals in an organisation are – everyone can make mistakes for e.g. improper maintenance which can lead to non-compliance.
The challenge is to develop an approach that removes the threat and creates the appropriate checks and balances to validate actions before errors occur.
This may mean removing human error from the equation.
Sectors where the cost of a human error exceeds the risk appetite of the organisation is unacceptable.
Risk appetite is the amount and type of risk that you are willing to take to meet your strategic objectives i.e. the general level of risk you accept and before any mitigating action is determined as necessary to reduce the risk.
For example, in the food manufacturing industry where food safety compliance and lost revenue through unscheduled maintenance and repair of production facilities is unacceptable.
Put simply, the key outcome of DLM is to reduce human error and to identify the optimal course of action, after considering all the relevant factors and using informed decision-making through access to good-quality data.
What Are The Advantages Of Digital-led Maintenance?
Provides Data-Driven Insights
Digital tools can collect and analyse vast sums of data, providing valuable insights into maintenance and business operations.
These insights inform decision-making, helping organisations to identify trends, optimise processes and uncover new opportunities.
improves Accuracy And Quality Assurance
As has been established, human error is inevitable and especially likely when carrying out repetitive tasks.
Digital-led maintenance can replace error-prone and time-consuming manual processes, ensuring consistency and precision.
It enables detailed process auditing and productivity reporting, and increased process accuracy improves output quality.
Reduces Costs
Automating repetitive tasks increases processing speed, improves accuracy and reduces the need for reworking, which in turn can reduce the need for manual labour and lead to significant cost savings.
Organisations can then reallocate these savings towards further investments in innovation.
Supports Compliance
Digital-led Maintenance can be programmed to adhere to regulatory requirements, ensuring compliance and mitigating risks associated with non-compliance.
Facilitates Integration and Scalability
Digital-led Maintenance can seamlessly integrate with existing systems without the need for extensive IT overhauls.
This flexibility allows organisations to scale their automation efforts rapidly, adapting to changing business needs and market conditions.
Accelerates Digital Initiatives
By automating core processes, Digital-led Maintenance accelerates the deployment of other digital technologies such as Artificial Intelligence (AI), Machine Learning (ML) and Internet of Things (IoT).
This synergy creates a robust digital ecosystem that can help to drive innovation and growth.
Enhances Efficiency And Productivity
DLM can automate repetitive, mundane and labour-intensive tasks and free up staff to focus on more value-added work.
More commonly known as Robotic Process Automation (RPA), this enhances the information processing speed and delivery to deliver more timely information and support decision making.
RPA offers improved services to processes that have a high probability of human error, such as repetitive data entry, thereby increasing accuracy and productivity.
Agility and Responsiveness
In a highly regulated or competitive environment, the ability to adapt quickly to changes in legislation or the market is crucial.
Automation and good quality data allow organisations to respond swiftly to regulatory updates, as well as market changes and customer demands, allowing organisations to maintain a competitive edge.
Enhanced Customer Experience
Technology enables faster and more accurate service delivery, improving customer satisfaction in the long run.
Whether it’s processing orders, handling inquiries or managing support tickets, better data processing and automation ensures timely and efficient responses.
What Are The Disadvantages of Digital-led Maintenance?
IWFM's guidance document titled “Harnessing the power of data” identified that there are two main types of barriers that organisations have to contend with before they can gain the benefits from DLM: technical and cultural.
Technical Barriers
In IWFM’s Guidance Note – Harnessing the power of Data, they gave examples of technical barriers, including:
- Data being stored in different systems and spreadsheets
- Legacy IT systems and processes datasets containing missing or inaccurate data
- Unstructured (qualitative) data stored in documents and other difficult-to-use formats.
However, such barriers are rarely difficult to solve from a technical point of view.
Often, the main constraint is the amount of time and money required to deal with technical barriers and whether such actions will lead to a sufficient Return on Investment (ROI).
Cultural Barriers
On the cultural side, the IWFM highlighted:
- A lack of awareness and understanding of data and the potential it can bring to a business
- The tendency for departments and managers to want to keep ‘their’ data to themselves (referred to as “siloed datasets”)
- Data being manipulated and presented to give answers that were expected by senior leaders, a lack of accountability, ownership and governance of corporate data people not trusting or being sceptical of data.
- Data being seen as an ‘IT problem’ rather than as a business asset
The last element is once more a human factor – the possible reluctance to accept and embrace change because it involves changes to people’s beliefs, attitudes and behaviours, which tend to be deeply ingrained and reinforced by an organisation’s rules, processes and structures.
To successfully navigate this path, you may require help from a skilled and experienced change manager.
It’s essential that staff are fully engaged in the process of adopting Digital-led Maintenance.
You’ll need to ensure that there is space for your team members to address their concerns and that you demonstrate the value of the technology and appropriately train them. This will help to ensure smooth adoption and to foster a positive attitude towards it.
Another challenge with adopting transformative technology is to be aware of when enough is actually enough.
You need to be clear on what outcomes you want to achieve and undertake a clear investment appraisal that looks at both capital and revenue costs over the whole life of the technology to calculate a realistic ROI.
How To Create A Business Case For Digital-led Maintenance In Your Organisation
The case for change from a traditional style of maintenance, whether that be reactive or proactive, to one that could be described as DLM needs to involve more than a reduction in human error.
Depending on the sector, the tolerance for risk can vary. Therefore, the case for change should be around value. The concept of value is much more complex than just cost.
When establishing whether it’s worth adopting a more data and technology focused approach, you need to make the investment decision based on the value you can reasonably expect to receive.
If you do decide to adopt products or services, use these questions to make value-focused decisions:
- What problems does this product or service address?
- How well does it align with my organisation’s needs?
- What results does this product or service claim to provide?
- What effort do I need to make to get those results?
- Am I willing and able to do that?
- What support is provided if I go for those results?
It's important to remember that while technology can achieve a great amount, you need to be clear on the value you want to get from it.
How To Implement Digital-led Maintenance In Your Organisation
Step 1: Assess Your Organisation’s Digital Maturity
Before commencing any digital transformation journey, an organisation should make a critical assessment of its digital maturity.
There are a number of publicly available standards that can help assess “digital readiness”.
This is the measure of the maturity of an organisation, or part of an organisation, in optimising its use of digital technologies by organising its resources and activities to make the best use of the right digital technologies and to drive value from them.
There are a great many other resources that can be accessed to help in a self-assessment exercise, including:
- British Standard Institution documents such as PAS 2009:2024 and PAS 1040:2019
Each have slightly different approaches and assessment criteria, and it is up to you to decide on which methodology you feel will provide a clear and honest picture.
The outcome should be that you can create a developmental route map to set up and support the delivery of your organisation's digital transformation.
Step 2: Find The Right Third-Party Partner
Once you have gone through some self-reflection and maybe some self-assessment on where you are on your digital journey, it’s time to make a decision on whether you can go it alone on implementing DLM or if you need the help of a third party.
This may be a software provider, consultant or other professional bodies. There are many consultancies out there who can fulfil the role of a digital partner.
You should have a reasonable idea of what benefits you want to gain from harnessing the power of data before you start, otherwise, it may be difficult to properly articulate a finite scope.
For those who do not want to go to that expense, help is at hand from many professional bodies such as BESA (The Building Engineering Services Association) and IWFM (The Institute of Workplace and Facilities Management) with guidance, tools and training.
We recommend reading the following documents:
- IWFM’s Guidance Note on "Harnessing the power of data"
- BESA’s work aligning SFG20 maintenance standards with the RICS New Rules of Measurement (NRM) for building works and the BIM Construction Classification (Uniclass) developed by NBS
- CIBSE’s (The Chartered Institution of Building Services Engineers) Guide M: best practice guidance for management and maintenance of engineering services
Step 3: Create a Digital Strategy
Once you know your starting state in terms of digital maturity and you have found the appropriate digital partner if required, you should look at creating a strategy and a delivery plan to leverage the power of digitisation and data.
This strategy should look at the end state/the level of maturity you want or will be comfortable with.
It should set clear goals and objectives and then identify the building blocks in order to achieve them.
This could look at the development of a new Target Operating Model or improve the elements within the existing operating model such as enhanced processes, upskilling people or recruiting people with the necessary competencies, or investing in new technologies.
Step 4: Implementation
To deliver the transformation in the timeline proposed, ensure to provide the necessary resources in terms of time, labour and money required.
There will also be a requirement to actively manage risks and measure progress through milestones.
Step 5: Audit and Assure Digital Strategy
When an organisation commences any transformation, it should always look at having a plan to audit and assure its transition.
There should be a clear set of goals and objectives that can be measured or a mechanism to measure progress. The original maturity assessment tool may be a mechanism by which this can be done.
Consideration should be given to who is best placed to measure your progress. It might be appropriate to request an independent third party to undertake the assessment to ensure that there is an unbiased opinion on the outcome.
Can Digital-led Maintenance Be Used On Its Own?
DLM moves beyond traditional maintenance towards more proactive, predictive approaches that support planned preventative maintenance (PPM).
However, it’s important to note that there is no one single solution to maintenance. Instead, a blend of different maintenance tactics should be applied that are site-specific based on the equipment installed and the risks that asset failure could cause in an organisation.
At SFG20, we advocate for a combined approach of PPM, DLM and other strategies to support the circular economy model, improve efficiency and help keep your organisation compliant.
It’s important to note that some PPM tasks cannot be fully replaced by DLM, for example, tasks associated with fire safety that require fixed inspections and manual (physical) operation of parts such as fire alarm installations.
Fire alarms are checked via a manual call point (break glass) or test point (similar to a magnetic door release) that must be physically operated and returned to its initial position. So, you’ll only know if it is faulty by operating the item.
Although fire alarms have some digital implementation, the industry is not yet at the stage of self-testing. Faults can be monitored, but the actual “physical test” requires undertaking.
Fire safety tasks can be traced to primary legislation which offers fixed maintenance tasks covering daily, weekly or monthly checks depending on the system, and is aimed at the “physical” approach.
Read Our Ultimate Guide To Compliance In Facilities Management
As you now know, Digital-led Maintenance is a blend of data alongside digital tools and platforms which, among many other benefits, principally aims to reduce human error, improve decision making and support compliance.
Before implementing Digital-led maintenance, you need to be both clear on your compliance responsibilities.
At SFG20, it’s our role to provide a trusted, legally compliant standard for organisations to adhere to in order to keep their buildings safe.
One of the ways in which we act upon this duty is by providing expert-backed educational resources such as our popular Ultimate Guide To Compliance which contains all of the essential information you need to know about your obligations.
To find out more, hit the button below.