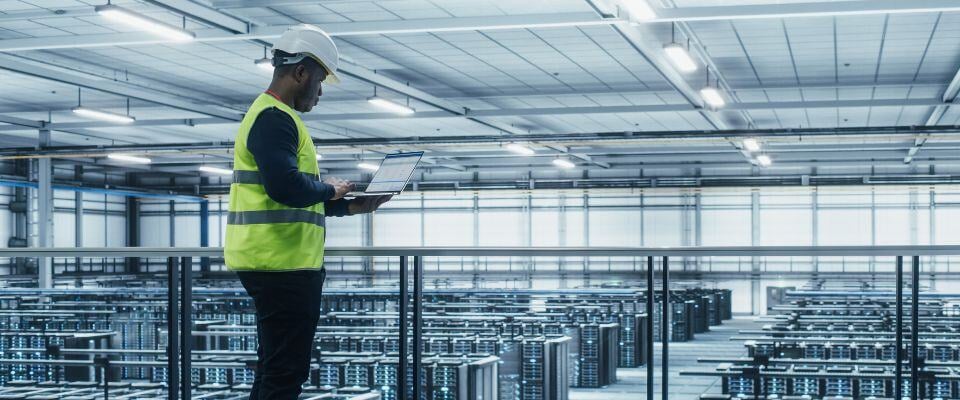
What Is Planned Preventative Maintenance?
Planned preventative maintenance (PPM) plays an integral role in prolonging and maintaining a building’s assets, resources, equipment, and infrastructure, and so it is a topic that all facilities managers (FM) and building owners need to understand fully.
As SFG20 has been the industry standard for building maintenance since 1990, we know what we’re talking about when it comes to PPM, so whether you’re a facilities manager or building owner needing advice, you’ve come to the right place.
In this guide, we’ll help you understand what planned preventative maintenance is, how it differs from reactive maintenance, why you need it, as well as the pros and cons you need to consider.
What is Planned Preventative Maintenance?
Planned preventative maintenance, often shortened to PPM, refers to a series of planned maintenance procedures carried out in line with current regulations, to help prolong the lifespan of an asset.
Assets count as anything in a building that must be maintained to keep it fit for purpose – so includes the building fabric (walls, floors, ceilings, roof and windows) and anything housed both within and around the building, such as HVAC electrical and fire systems.
Critical Assets (also known as life critical systems) - such as a back-up generator, fire alarm system or sprinkler system are critical items that will have a detrimental impact if they fail to operate.
A good PPM routine is achieved by carrying out regular inspection and testing in compliance with the current regulations.
The thought process behind it is that prevention is better than cure; acting sooner rather than later before anything goes wrong.
You may have heard of reactive maintenance, which is essentially the opposite of PPM and involves fixing issues as and when they happen.
There is a place for both approaches and, in some cases, reactive maintenance is the better option. For example, if you have a light fitting with a faulty bulb, you couldn’t have prevented it from failing; there’s no way of maintaining a lamp to make it last longer, and it’s something that’s easily replaced.
Why do I need Planned Preventative Maintenance?
There are several reasons why PPM is such an essential part of building maintenance, some of which are based on cost effectiveness, but there’s also legal compliance to take into consideration.
Here are some examples of why you need PPM:
Compliance
Health and safety is a serious subject and ignoring non-compliance within a building could pose a serious risk to people.
It’s not only immoral, but illegal too.
Failing to adhere to current regulations, whether that’s fire, electrical and gas safety or controlling the risk of accidents, can result in penalties and fines.
Improved safety and productivity in the workplace
Of course, saving money is a great benefit of PPM, but ultimately the safety of the people in the building day in and day out is the most important thing of all.
There’s also staff productivity to consider too; for example, an HVAC system that doesn’t work properly can create an uncomfortable environment that affects a worker’s productivity levels.
Equipment longevity
Carrying out a comprehensive maintenance routine helps prevent equipment downtime from faults or failures.
Regular inspection and testing will help equipment operate correctly and efficiently and capture any issues that may be arising. Any repairs needed can then be arranged accordingly.
Keeping equipment working properly for longer will help save money in the long run and make expensive breakdowns less likely.
Carbon Emission Reduction
Well maintained assets not only last longer, but they also use less energy too because they can operate more efficiently. This helps Maintenance teams reduce operational and embodied carbon emissions.
Prevents smaller problems from escalating to larger ones
A PPM is undertaken to keep equipment running correctly and to ensure that any issues spotted are reported and dealt with before they become a problem.
Budgeting
Every business will have a yearly budget and while there’s no way to predict every expenditure that will come your way, knowing what tasks need to be undertaken and when they are due, means you can pre-plan maintenance budgets accordingly.
What are the Pros and Cons of Planned Preventative Maintenance?
Below is a summary of the advantages and disadvantages of PPM:
Pros
- Long-term maintenance costs are reduced
- Prevent escalating maintenance costs by identifying issues early
- Helps prevent downtime and delays
- Keeps equipment running efficiently
- Increases safety
- Reduces overall energy consumption
Cons
- Short term time investment to set up
- Short term cost increase
- Staff training
What are the different types of Planned Preventative Maintenance?
So, now that you know what PPM is and why you should put it into practice, let's take a look at the different types so you can implement them effectively.
Predictive maintenance
Predictive Maintenance is a strategy based on data analysis combined with real-time data to help predict any potential problems – repairs can be carried out before a complete failure occurs, saving both time and money.
This can be a useful method for specialised equipment. Say you have a production line that fails to work if it overheats – by monitoring the temperature levels you’ll know if it needs maintenance before it stops working completely.
By knowing beforehand, you can schedule the maintenance accordingly.
Condition-based maintenance
With Condition-based Maintenance (CBM), sensors and other monitoring equipment are used to analyse and assess the condition of assets in real time.
Examples of what this would be useful for include:
- HVAC systems – thermographic surveys (thermal imaging) can look for issues like leaks and blocked ducts.
- Pipes – pressure levels can be monitored to avoid leaks.
- Computers – you can avoid overheating issues via temperature monitoring.
Risk-based maintenance
Risk-based Maintenance (RBM) works by prioritising maintenance resources for the assets that carry the most risk if they fail.
High-risk assets vary with site-specific requirements and the level of impact on a business.
Collecting data and using predictive tools can help to determine and categorise which assets are high risk – that way you can focus more on these areas to prevent issues that could have widespread consequences on a business.
Prescriptive maintenance
Prescriptive Maintenance is achieved through machine learning (ML) and Artificial Intelligence (AI), which collect data to predict possible equipment failures and then suggest specific maintenance actions to solve issues.
It’s a useful method for maintaining complex equipment used in sectors such as manufacturing, transportation, aerospace, energy, oil and gas and healthcare.
It can seem daunting, but creating a schedule for all these types of maintenance doesn’t need to be difficult.
Understand Your Compliance Responsibilities
So, you’ve now learnt the fundamentals of PPM and why it’s essential for any facilities manager or building owner. What’s more, you now know that carrying out PPMs in line with current regulations will create a safer environment and increase the longevity of assets.
With SFG20 being the industry standard for building maintenance specification, it’s our duty to ensure that those in the industry are not only well-informed but are also given the right tools to receive the best support possible.
If you would like to learn more, whether that’s understanding your compliance responsibilities or building maintenance strategies, our Ultimate Guide To Compliance in Facilities Management can help you.