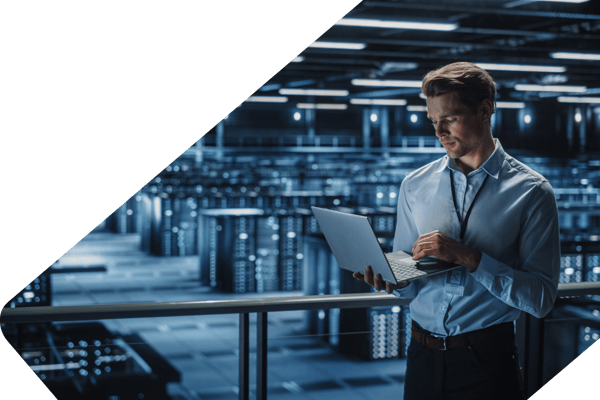
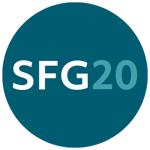
Planned preventative vs. reactive maintenance
When it comes to building and asset maintenance, there are many approaches to take, but two of the most widely used are planned preventative and reactive. Of course, this naturally fuels the ‘planned preventative vs reactive maintenance’ debate and it’s something businesses have to consider when establishing and implementing maintenance plans.
So, when discussing planned preventative vs reactive maintenance, which is considered to be the best? While there are varied opinions about this topic and companies who prefer one or the other, we’re going to take a look into both practices and discuss their pros and cons.
What is planned preventative maintenance?-Nov-03-2023-09-59-47-4008-AM.png?width=400&height=400&name=Template-1%20(1)-Nov-03-2023-09-59-47-4008-AM.png)
‘Planned maintenance’ is a term used to describe forms of maintenance designed to prolong the lifespan of assets, resources, equipment and a business’s infrastructure. Also, it offers the means to prevent the breakdown and malfunction of equipment and the expenses and downtime it incurs. For some, planned maintenance can be simple tasks such as cleaning and monitoring asset conditions. Whereas for others, it can consist of more complex tasks such as replacing parts or repairs.
While planned maintenance has been practised for many years, it has advanced considerably with the evolution of technology. Today, businesses have a wealth of tools and services available to them to increase maintenance efficiency and productivity while reducing the costs involved.
Pros of planned preventative maintenance
1) Minimise downtime
Preventing downtime, delays and ensuring daily operations are running at all times is essential for any business. Doing so maximises profits, increases business growth, and maintains a good brand reputation. And it just so happens that reducing and preventing downtime is one of the critical benefits of planned maintenance.
Planned maintenance helps maximise the uptime of assets and prevents significant, unforeseen repairs and breakdowns. These types of incidents cost more and are a headache for facility managers, as they can take longer to remedy whilst spare parts are being ordered and unforeseen works are scheduled into contractors’ already-full diaries. During this time, your facility will either have to close or operate at sub-optimal capacity. Planned preventative maintenance schedules can be used to define the maintenance plan for a building or estate.
2) Increase safety
Safety is a primary objective for all organisations, and maintenance is a vital aspect of establishing, maintaining and improving workplace safety. Planned maintenance schedules provide various benefits regarding safety, such as reducing malfunctions and deterioration of assets, protecting from health hazards, and avoiding liability lawsuits.
These risks - and more - can be avoided with planned maintenance, as you'll be able to implement a compliant, regular, reliable and effective maintenance regime. Meaning you'll be aware of safety or efficiency concerns more quickly and have the ability to act right away and prevent hazards.
3) Reduce costs & energy consumption
Planned maintenance and its benefits can save businesses money. As you will always be aware of when maintenance will occur and needs to happen, you'll never use systems and equipment to the point of failure. Meaning you'll also avoid the significant expense it leads to, and organisations who invest in planned maintenance experience less breakdowns and fewer disruptions to their business. Of course, this saves money on large-scale repairs and maximises profits through minimal downtime.
Another critical factor to consider is energy consumption. Poorly maintained electrical assets or malfunctioning equipment consume more energy than those that operate as they should. Planned maintenance and proactive scheduling ensure facility managers identify issues early on and address them as soon as possible. By doing so, they avoid crippling energy bills and adopt more environmentally-friendly practices.
Cons of planned preventative maintenance
1) The need for effective planning
One area that may prove a challenge for some organisations is an increased need for planning (as the name suggests). Fortunately, planned maintenance software can support facility managers with effective scheduling.
2) Initial costs:
Compared to reactive maintenance, planned maintenance does require more initial financial investment during the setup and implementation stages. This can put some people off. However, it's important to remember that you'll be spending more money now to ensure your assets operate efficiently and for their full lifespan, minimising costly replacement of equipment.
What is reactive maintenance?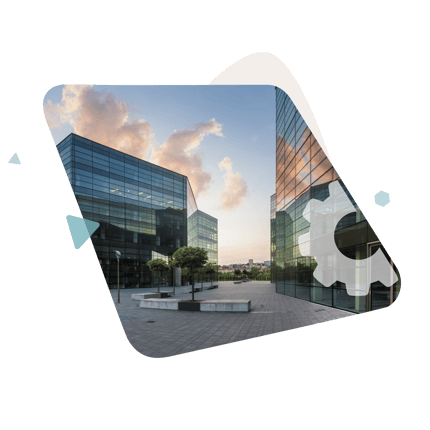
As you can guess from the name, reactive maintenance is performed when an asset has broken down or is underperforming — maintenance as a ‘reaction’ to an issue. Reactive maintenance is important for restoring or replacing broken equipment and ensuring business operations are up and running without delay or additional problems.
However, reactive maintenance isn’t always the most efficient approach, as a great deal of the maintenance issues businesses face can be prevented with planned maintenance. This exact point is essentially the foundation of the planned preventative vs reactive maintenance debate. And while reactive maintenance can assume a role within a business’s maintenance plan, it should never be considered to be your primary solution for maintaining your facility.
Pros of reactive maintenance
1) Minimise downtime:
Preventing downtime, delays and ensuring daily operations are running at all times is essential for any business. Doing so maximises profits, increases business growth, and maintains a good brand reputation. And it just so happens that reducing and preventing downtime is one of the critical benefits of planned maintenance. Planned maintenance helps maximise the uptime of assets and prevents significant, unforeseen repairs and breakdowns. These types of incidents cost more and are a headache for facility managers, as they can take longer to remedy whilst spare parts are being ordered and unforeseen works are scheduled into contractors’ already-full diaries. During this time, your facility will either have to close or operate at sub-optimal capacity.
Planned preventative maintenance schedules can be used to define the maintenance plan for a building or estate.
2) Increase safety
Safety is a primary objective for all organisations, and maintenance is a vital aspect of establishing, maintaining and improving workplace safety. Planned maintenance schedules provide various benefits regarding safety, such as reducing malfunctions and deterioration of assets, protecting from health hazards, and avoiding liability lawsuits.
These risks - and more - can be avoided with planned maintenance, as you'll be able to implement a compliant, regular, reliable and effective maintenance regime. Meaning you'll be aware of safety or efficiency concerns more quickly and have the ability to act right away and prevent hazards.
3) Reduce costs & energy consumption
Planned maintenance and its benefits can save businesses money. As you will always be aware of when maintenance will occur and needs to happen, you'll never use systems and equipment to the point of failure. Meaning you'll also avoid the significant expense it leads to, and organisations who invest in planned maintenance experience less breakdowns and fewer disruptions to their business. Of course, this saves money on large-scale repairs and maximises profits through minimal downtime.
Another critical factor to consider is energy consumption. Poorly maintained electrical assets or malfunctioning equipment consume more energy than those that operate as they should. Planned maintenance and proactive scheduling ensure facility managers identify issues early on and address them as soon as possible. By doing so, they avoid crippling energy bills and adopt more environmentally-friendly practices.
Cons of reactive maintenance
1) The need for effective planning:
One area that may prove a challenge for some organisations is an increased need for planning (as the name suggests). Fortunately, planned maintenance software can support facility managers with effective scheduling.
2) Initial costs:
Compared to reactive maintenance, planned maintenance does require more initial financial investment during the setup and implementation stages. This can put some people off. However, it's important to remember that you'll be spending more money now to ensure your assets operate efficiently and for their full lifespan, minimising costly replacement of equipment.