What Is IoT Technology? How It Works, Examples, Pros & Cons
Outdated asset tracking methods such as spreadsheets and paper forms can be hugely impractical. This is especially true as your estate grows and manually updating your plans becomes unwieldy, time-consuming and prone to human error, which could lead to non-compliance.
At SFG20, the industry standard for building maintenance since 1990, we've always prioritised building safety and compliance. That's why we're excited to explore how IoT technology can assist with building safety and pass on this knowledge to you so that your organisation can use it to the best possible advantage.
Below, we’ll give you an overview of what IoT technology is and how it works alongside examples before weighing all of its pros and cons.
What Is IoT Technology? 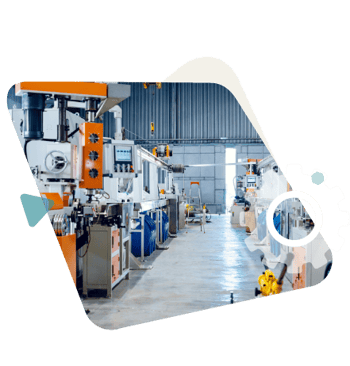
IoT (Internet of Things) technology refers to a network of physical objects embedded with sensors that communicate with each other to provide real-time data and insights about a building's systems and operations.
This technology allows building owners and facility managers to remotely monitor, control and optimise various aspects of a building, helping to inform maintenance decisions, optimise resource allocation and predict potential failures.
Many smart building management systems (BMS) integrate with Internet of Things (IoT) technology to monitor and control building operations in real time, enabling facilities to respond to issues immediately as well as help to improve the comfort, safety and reliability of assets for both building owners and occupants.
How Does IoT technology Work In Buildings?
- IoT sensors are installed throughout the building and directly connected to physical objects to collect data such as temperature, humidity, air quality, light, motion and how efficiently an asset may be operating.
- Collected data is then transmitted using methods such as wireless and Bluetooth to a central system such as a CMMS (Computerised Maintenance Management System) or a cloud platform.
- Advanced analytics, often powered by AI and machine learning, process the data to derive actionable insights and identify any patterns or anomalies.
- Based on the analysed data, the system can automatically adjust building systems (for example, HVAC or lighting) and be programmed to trigger alerts for any required maintenance works or issues.
- Facility managers and Building Owners can access the processed data and insights through a centralised dashboard, allowing for easy monitoring. This simple process also helps to speed up decisions and process issues.
Examples Of IoT Sensors For Building Maintenance
Temperature Monitoring
Temperature sensors monitor the operational temperature of an asset in real time, allowing maintenance teams to react to potential issues such as overheating.
This proactive approach can help to avoid costly breakdowns and extend the lifespan of an asset.
Vibration Monitoring
Vibration sensors are used to monitor excessive movement which can be caused by loose or faulty equipment associated with plant and machinery.
If not monitored, vibrations can cause major problems, for example, bolts or fixings may sheer or loosen severely.
By analysing vibration patterns, faults and defects can be picked up and maintenance can be scheduled before critical issues arise, reducing unplanned downtime.
Flow Sensors
Flow sensors monitor the movement of fluids through pipes and equipment.
By accurately measuring flow rates, these sensors can help maintenance personnel to identify potential problems such as blockages or pump degradation and in doing so reduce disruptive downtime.
Humidity Sensors
Humidity sensors allow maintenance teams to monitor and control relative humidity levels to prevent issues such as mould growth, corrosion and moisture build-up.
The degradation of electronic components can result in the shutdown of critical equipment, so if not properly managed, it can have severe consequences.
Pressure Sensors
Pressure sensors for equipment such as boilers, hydraulic systems and industrial pipelines enable maintenance teams to detect subtle changes in pressure levels and allow for early identification of issues e.g. leaks, clogs or valve malfunctions.
HVAC System Monitoring
IoT sensors integrated into heating, ventilation and air conditioning (HVAC) systems can provide real-time data on performance, energy consumption, fault monitoring and environmental changes.
This enables Facility Managers to optimise energy usage and monitor how rooms are being used by occupants so that parameters can be adjusted accordingly.
They allow faults to be picked up quickly and efficiently before they lead to costly and disruptive system failures.
What Are The Advantages Of IoT Monitors And Sensors?
Enhances Safety And Reliability
IoT sensors may also be able to identify potential hazards before they occur, helping to prevent severe breakdowns or even accidents.
By continuously monitoring critical parameters such as temperature, vibration and pressure, maintenance teams can ensure that equipment is operating not only effectively but also safely.
Saves Energy And Money
Implementing IoT sensors can offer major energy and cost-saving benefits for heating, cooling, ventilation and lighting systems.
This is because sensor technology monitors assets consistently to ensure that they are operating efficiently and as per their design and that potential issues can be pinpointed with haste.
More specially, using IoT technology to monitor and manage high-usage, energy-intensive assets can have a significant environmental impact.
Reduces Downtime 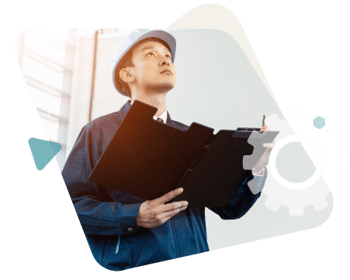
As IoT sensors provide continuous, real-time monitoring of equipment and their performance, this allows maintenance teams to identify potential issues before they turn into major problems which can lead to asset downtime.
Extends Asset Lifespan
Continuous monitoring enables Facility Management teams to find anomalies and track the reliability and performance of assets to ensure that they are still delivering what they were originally designed to do.
This also ensures that maintenance is performed only when necessary, saving time and money while optimising maintenance activities. In turn, this will help to improve asset performance, reliability and ultimately its lifespan.
Data-Driven Decision Making
IoT smart sensors collect data which can be analysed to identify patterns and trends.
This data can then be used to build and develop a site-specific maintenance plan, enabling facility managers to prioritise critical assets and make informed decisions about resource allocation, maintenance schedules as well as replacements and repairs.
Frees Up Time
As visual inspections can be supplemented by remote monitoring using IoT-enabled sensors, this can eliminate unnecessary trips and free up engineers’ time to focus on more critical tasks.
What Are The Disadvantages Of IoT Monitors And Sensors?
Risk Of Non-compliance
As legislation and regulations are constantly evolving, over-reliance on IoT sensors may lead to non-compliance.
That’s why at SFG20, we advocate for a blended approach of maintenance strategies including Planned Preventive Maintenance (PPM).
Overreliance On Technology
While sensor technology can be largely relied on, it’s not always 100% accurate.
If a sensor fails, a fault or breakdown may not be registered.
This is why maintaining sensors and checking that they are operating correctly is equally as important.
Cybersecurity Concerns
Internet-connected sensors and monitors can introduce new cybersecurity risks if not properly secured.
For example, there is the risk that hackers could access sensitive operational data or even take control of systems if proper security measures are not in place.
Technical Challenges
For some organisations, deploying and managing an integrated and connected system can come with technical hurdles.
Interpreting large amounts of data generated by sensors and monitors requires expertise that many businesses lack, meaning you may need to spend time developing the necessary skills within your team.
Stay Ahead Of The Future Of FM Software
As we’ve explored, IoT-enabled sensors and monitors can unlock many doors for organisations in terms of saving time, energy and money, all while reducing downtime and increasing asset lifespan.
Sensors and monitors represent just one building block of Digital-led Maintenance. Further advanced technologies such as AI, Digital Twins and Augmented Reality (AR) have emerged to help create safer and more efficient working environments for the building maintenance sector.
At SFG20, our mission is to help you succeed in creating and maintaining safer buildings that are not only compliant but also fit for the future.
Want to stay one step ahead of the curve? By clicking below, you’ll be taken to our definitive guide to Digital-led maintenance which will give you all the steps you need to implement new and emerging transformative technologies within your organisation.